Three maintenance centers for storing and maintaining our vehicles
tpg has three main sites ideally located for our network.
For a public transport company, building location – especially for large vehicle depots and maintenance centers – is extremely important, both in terms of operational efficiency and cost optimization. As a result, our maintenance centers are located at key points on our network.
Bachet-de-Pesay
Built in 1992, the Bachet-de-Pesay site houses the tpg’s head office and administration, as well as a depot and maintenance center for tramways and buses. It brings together, over 53,500 square meters and 3 levels, office employees, drivers, and employees in charge of vehicle maintenance. It consists of:
- the depot and the maintenance and repair workshops for tramways and buses;
- a 622-meter-long test track (tramway, trolley and bus);
- a tpg sales agency;
- all administrative premises for all areas of activity, including general management and the Board of Directors.
Truly committed to sustainable development, tpg produces a large part of the energy they consume thanks to the solar panels that cover part of the Bachet roof.

Jonction
The former headquarters of the CGTE and tpg, the Jonction site houses over more than 42,558 m2, some administrative services, including those related to driver training, the depot and maintenance workshops for trolleybuses and buses.
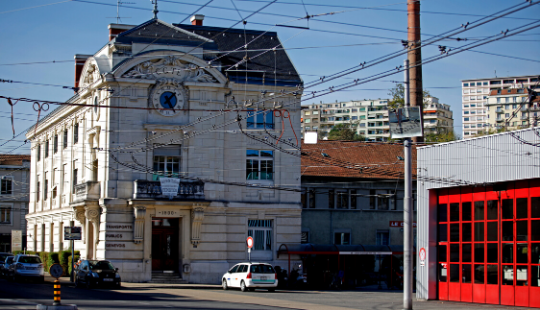
En Chardon
The third tpg maintenance center and depot, En Chardon site, went into full operation on October 26, 2020.
It is intended to accompany the future extension of tpg network. It will ensure a presence of tpg on Geneva’s right bank. This will allow for better vehicle distribution throughout the canton. It will also meet the requests from the State of Geneva to free up the Pointe de la Jonction, where part of our bus fleet was parked.
Located in Vernier on the tramway axis towards CERN, En Chardon now houses a large part of tpg fleet over a surface of 33,000 m². The total capacity, spread over three levels (two of which are underground), amounts to 70 tramways and 130 articulated buses in closed storage halls, allowing for regular maintenance. The roof houses a 5,000 m² photovoltaic solar power plant and a 15,000 m² green area.
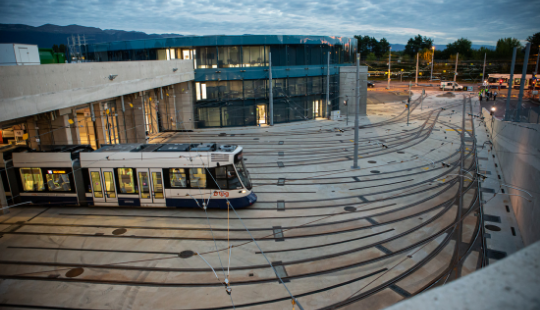
This is an extraordinary site that respects the principles of sustainable development
The Maintenance center’s location requires a very specific architecture, since the height of the building must be lower than the air ceiling. The part of the depot located in this area was therefore built underground; the main roof of the building rises to about 5 m on the side of the road to Meyrin and barely 80 cm on the side of the road to Champs-Prévost. The roofs have been designed to accommodate a photovoltaic solar power plant totaling approximately 5,000 m². The remaining 15,000 m² of roofs will be converted into green spaces.
En Chardon site is resolutely respectful of the principles of sustainable development, as shown by the choice of location, which allows for the development of an almost unusable piece of land located at the end of the runway of Geneva Airport and the building’s type of construction, which meets high ecological standards, in particular by being designed to obtain the Minergie label. Thus, tpg, in collaboration with Implenia (civil engineering), built and put into service a 1.6 km long conveyor belt to evacuate waste from the construction site to the Epeisses gravel pit, where it would be recycled.
The evacuation structure was mainly aerial, with the exception of a 90 m section buried under the SBB tracks near the construction site. It allowed for the evacuation of 325,000 m3 of excavated material out of a total of 505,000 m3 (the rest being transported by truck). This was a CHF 6 million project. By favoring this method of transporting waste over the more traditional road transport, we have helped the environment in two ways: by limiting the use of heavy goods vehicles, we have avoided overloading individual motorized traffic in the sector and have as a result also reduced CO2 emissions. Transport by conveyor belt compensated for 30,000 truck trips with a carbon footprint three times lower than if the evacuation had been done by road.